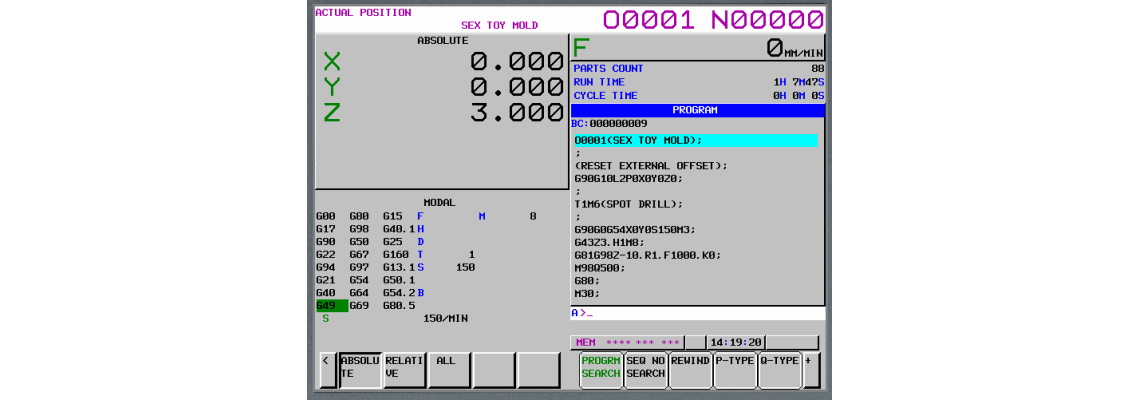
CNC (computer numerical control) programming is the process of creating a program, or set of instructions, for a CNC machine to execute a specific task, such as cutting or drilling a part. These instructions are typically written in a programming language such as G-code or M-code, and are then loaded into the CNC machine's controller, which interprets and executes the instructions to control the machine's movements.
The basics of CNC programming include:
Understanding the machine's capabilities and limitations: Before writing a program, it's important to understand the specific capabilities and limitations of the CNC machine you will be using. This includes understanding the machine's axis of motion, maximum feed rates, and maximum cutting speeds.
Creating a part model or blueprint: In order to program a CNC machine, you will need to have a detailed model or blueprint of the part you want to produce. This can be created using computer-aided design (CAD) software.
Generating toolpaths: Once you have a model of the part, you will need to generate the toolpaths, which are the specific paths that the cutting tool will follow. This can be done using computer-aided manufacturing (CAM) software.
Writing the program: After the toolpaths are generated, the next step is to write the program in G-code or M-code, which is the language that the CNC machine understands.
Testing the program: Before running the program on the machine, it's important to test and verify that the program is correct. This can be done by simulating the program on the computer, or by running the program on a test piece of material.
Running the program on the machine: Once the program is verified, it can be loaded into the CNC machine's controller and executed to produce the part.
Monitoring the machine: Lastly, it is important to monitor the machine during the production process, checking for any errors or issues that may arise, and making any necessary adjustments.
Leave a Comment